Multiplex bestaat uit drie of meer dunne houtlagen die met een lijm aan elkaar zijn gelijmd. Elke houtlaag, of multiplex, is meestal zo georiënteerd dat de nerf haaks op de aangrenzende laag staat om krimp te verminderen en de sterkte van het eindproduct te verbeteren. De meeste multiplex wordt geperst tot grote, vlakke platen die in de bouw worden gebruikt. Andere multiplexstukken kunnen worden gevormd tot eenvoudige of samengestelde krommingen voor gebruik in meubels, boten en vliegtuigen.
Het gebruik van dunne houtlagen als constructiemateriaal dateert van ongeveer 1500 v.Chr., toen Egyptische ambachtslieden dunne stukjes donker ebbenhout aan de buitenkant van een cederhouten kistje lijmden, gevonden in het graf van koning Toetanchamon. Deze techniek werd later door de Grieken en Romeinen gebruikt om fijn meubilair en andere decoratieve objecten te produceren. In de 17e eeuw werd de kunst van het decoreren van meubels met dunne stukjes hout bekend als fineren, en de stukken zelf werden fineer genoemd.
Tot eind 18e eeuw werden de stukken fineer volledig met de hand gesneden. In 1797 vroeg de Engelsman Sir Samuel Bentham patenten aan voor verschillende machines voor de productie van fineer. In zijn patentaanvragen beschreef hij het concept van het lamineren van meerdere lagen fineer met lijm om een dikker stuk te vormen – de eerste beschrijving van wat we nu multiplex noemen.
Ondanks deze ontwikkeling duurde het bijna honderd jaar voordat gelamineerd fineer commerciële toepassingen vond buiten de meubelindustrie. Rond 1890 werd gelamineerd hout voor het eerst gebruikt voor de productie van deuren. Naarmate de vraag toenam, begonnen verschillende bedrijven platen van meerlaags gelamineerd hout te produceren, niet alleen voor deuren, maar ook voor gebruik in treinwagons, bussen en vliegtuigen. Ondanks dit toegenomen gebruik creëerde het concept van "geplakt hout", zoals sommige ambachtslieden het sarcastisch noemden, een negatief imago voor het product. Om dit imago tegen te gaan, kwamen de fabrikanten van gelamineerd hout bijeen en kozen uiteindelijk voor de term "multiplex" om het nieuwe materiaal te beschrijven.
In 1928 werden de eerste multiplexplaten van 1,2 bij 2,4 meter (4 bij 8 voet) in standaardformaat in de Verenigde Staten geïntroduceerd voor gebruik als algemeen bouwmateriaal. In de daaropvolgende decennia maakten verbeterde lijmsoorten en nieuwe productiemethoden het mogelijk om multiplex voor een breed scala aan toepassingen te gebruiken. Tegenwoordig vervangt multiplex gezaagd hout voor vele bouwdoeleinden en is de multiplexproductie uitgegroeid tot een wereldwijde miljardenindustrie.
De buitenste lagen van multiplex worden respectievelijk de voorkant en de achterkant genoemd. De voorkant is het oppervlak dat gebruikt of zichtbaar is, terwijl de achterkant ongebruikt of verborgen blijft. De middelste laag wordt de kern genoemd. Bij multiplex met vijf of meer lagen worden de tussenliggende lagen de dwarsbanden genoemd.
Multiplex kan gemaakt worden van hardhout, zachthout of een combinatie van beide. Enkele veelvoorkomende hardhoutsoorten zijn essenhout, esdoornhout, mahoniehout, eikenhout en teakhout. Douglasspar is het meest gebruikte zachthout voor multiplex in de Verenigde Staten, hoewel er ook verschillende soorten grenenhout, cederhout, sparrenhout en redwood worden gebruikt.
Composiet multiplex heeft een kern van spaanplaat of massief hout, die rand aan rand zijn verbonden. Het is afgewerkt met een multiplex fineerlaag aan de voor- en achterkant. Composiet multiplex wordt gebruikt waar zeer dikke platen nodig zijn.
Het type lijm dat gebruikt wordt om de houtlagen aan elkaar te lijmen, hangt af van de specifieke toepassing van het afgewerkte multiplex. Zachthouten multiplexplaten die ontworpen zijn voor installatie aan de buitenkant van een constructie, gebruiken meestal een fenolformaldehydehars als lijm vanwege de uitstekende sterkte en vochtbestendigheid. Zachthouten multiplexplaten die ontworpen zijn voor installatie aan de binnenkant van een constructie, kunnen een bloedproteïne- of sojabonenproteïnelijm gebruiken, hoewel de meeste zachthouten binnenplaten tegenwoordig gemaakt worden met dezelfde fenolformaldehydehars als buitenplaten. Hardhouten multiplex dat gebruikt wordt voor binnentoepassingen en de constructie van meubels, wordt meestal gemaakt met een ureumformaldehydehars.
Sommige toepassingen vereisen multiplexplaten met een dunne laag kunststof, metaal of met hars geïmpregneerd papier of textiel, verlijmd aan de voor- of achterkant (of beide) om het buitenoppervlak extra vocht- en slijtvast te maken of de verf beter te laten hechten. Dergelijk multiplex wordt overlay multiplex genoemd en wordt veel gebruikt in de bouw, transport en landbouw.
Andere multiplexplaten kunnen worden gecoat met een vloeibare beits om de oppervlakken een afgewerkte uitstraling te geven, of kunnen worden behandeld met verschillende chemicaliën om de brandwerendheid of weerstand tegen rotting van het multiplex te verbeteren.
Er zijn twee brede klassen multiplex, elk met zijn eigen classificatiesysteem.
Eén klasse staat bekend als bouw- en industriemultiplex. Multiplex in deze klasse wordt voornamelijk gebruikt vanwege zijn sterkte en wordt beoordeeld op basis van zijn blootstellingsvermogen en de fineerkwaliteit die op de voor- en achterkant wordt gebruikt. De blootstellingscapaciteit kan binnen of buiten zijn, afhankelijk van het type lijm. Fineerkwaliteiten kunnen N, A, B, C of D zijn. Kwaliteit N heeft zeer weinig oppervlaktedefecten, terwijl kwaliteit D talrijke knoesten en scheuren kan bevatten. Multiplex dat bijvoorbeeld wordt gebruikt als ondervloer in een huis, heeft de classificatie "Interior CD". Dit betekent dat het een C-zijde en een D-achterkant heeft en dat de lijm geschikt is voor gebruik op beschermde locaties. De binnenlagen van al het bouw- en industriemultiplex zijn gemaakt van fineer van klasse C of D, ongeacht de classificatie.
De andere klasse multiplex staat bekend als hardhout en decoratief multiplex. Multiplex in deze klasse wordt voornamelijk gebruikt vanwege het uiterlijk en wordt in afnemende mate van vochtbestendigheid geklasseerd als Technisch (Buiten), Type I (Buiten), Type II (Binnen) en Type III (Binnen). De fineerlagen zijn vrijwel vrij van gebreken.
Maten
Multiplexplaten variëren in dikte van 1,6 mm tot 76 mm. De meest voorkomende diktes liggen tussen 6,4 mm en 19 mm. Hoewel de kern, de dwarsbalken en de voor- en achterkant van een multiplexplaat uit fineer van verschillende diktes kunnen bestaan, moet de dikte van elk fineer rond het midden gelijk zijn. Zo moeten de voor- en achterkant even dik zijn. Ook de boven- en onderkant moeten even dik zijn.
De meest voorkomende afmetingen voor multiplexplaten in de bouw zijn 1,2 m breed en 2,4 m lang. Andere gangbare breedtes zijn 0,9 m en 1,5 m. De lengtes variëren van 2,4 m tot 3,6 m, in stappen van 0,3 m. Speciale toepassingen, zoals de botenbouw, kunnen grotere platen vereisen.
De bomen die gebruikt worden voor de productie van multiplex hebben over het algemeen een kleinere diameter dan de bomen die gebruikt worden voor de productie van timmerhout. In de meeste gevallen zijn ze geplant en gekweekt in gebieden die eigendom zijn van het multiplexbedrijf. Deze gebieden worden zorgvuldig beheerd om de boomgroei te maximaliseren en schade door insecten of brand te minimaliseren.
Hier is een typische volgorde van bewerkingen voor het verwerken van bomen tot standaard multiplexplaten van 1,2 m bij 2,4 m:
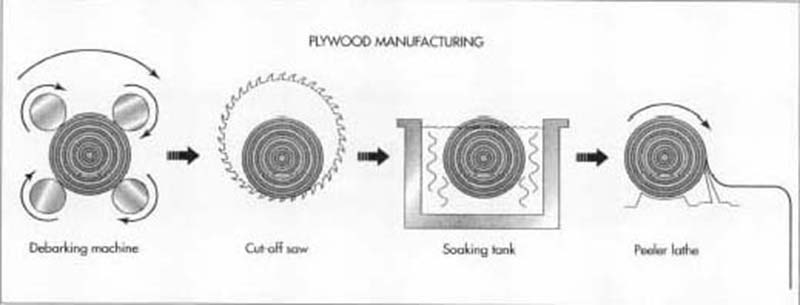
De boomstammen worden eerst ontschorst en vervolgens in schilblokken gesneden. Om de blokken in fineerstroken te snijden, worden ze eerst geweekt en vervolgens in stroken geschild.
1 Geselecteerde bomen in een gebied worden gemarkeerd als klaar om te worden gekapt. Het kappen kan worden gedaan met benzineaangedreven kettingzagen of met grote hydraulische scharen die aan de voorkant van wielvoertuigen zijn gemonteerd, zogenaamde fellers. De takken worden met kettingzagen van de omgevallen bomen verwijderd.
2 De gesnoeide boomstammen, oftewel boomstammen, worden door wielvoertuigen, skidders genaamd, naar een laadruimte gesleept. De boomstammen worden op lengte gezaagd en op vrachtwagens geladen voor transport naar de multiplexfabriek, waar ze in lange stapels worden gestapeld, zogenaamde houtstapels.
3 Wanneer er boomstammen nodig zijn, worden ze door laders met rubberen banden van de houtstapels gehaald en op een kettingtransportband gelegd die ze naar de ontschorsingsmachine brengt. Deze machine verwijdert de schors met behulp van slijpschijven met scherpe tanden of met hogedrukreinigers, terwijl de boomstam langzaam om zijn lengteas draait.
4 De ontschorste boomstammen worden op een kettingtransportband naar de zagerij gebracht, waar een enorme cirkelzaag ze in stukken van ongeveer 2,5 tot 2,6 meter lang zaagt, geschikt voor de productie van standaard platen van 2,4 meter lang. Deze stukken hout staan bekend als schilblokken.
5 Voordat het fineer gesneden kan worden, moeten de blokken worden verhit en geweekt om het hout zachter te maken. De blokken kunnen gestoomd of ondergedompeld worden in heet water. Dit proces duurt 12-40 uur, afhankelijk van de houtsoort, de diameter van het blok en andere factoren.
6 De verwarmde schilblokken worden vervolgens naar de schildraaibank getransporteerd, waar ze automatisch worden uitgelijnd en één voor één in de draaibank worden ingevoerd. Terwijl de draaibank het blok snel om zijn lengteas draait, pelt een mes over de volledige lengte een doorlopend vel fineer van het oppervlak van het draaiende blok met een snelheid van 90-240 m/min. Wanneer de diameter van het blok is teruggebracht tot ongeveer 230-305 mm, wordt het resterende stuk hout, de schilkern, uit de draaibank geworpen en wordt een nieuw schilblok geplaatst.
7 Het lange fineervel dat uit de schilmachine komt, kan direct worden verwerkt, of worden opgeslagen in lange trays met meerdere niveaus of op rollen worden gewikkeld. In elk geval bestaat het volgende proces uit het snijden van het fineer in bruikbare breedtes, meestal ongeveer 1,4 m, voor de productie van standaard multiplexplaten van 1,2 m breed. Tegelijkertijd zoeken optische scanners naar delen met onaanvaardbare defecten, die worden weggeknipt, waardoor er stukken fineer overblijven die kleiner zijn dan de standaardbreedte.
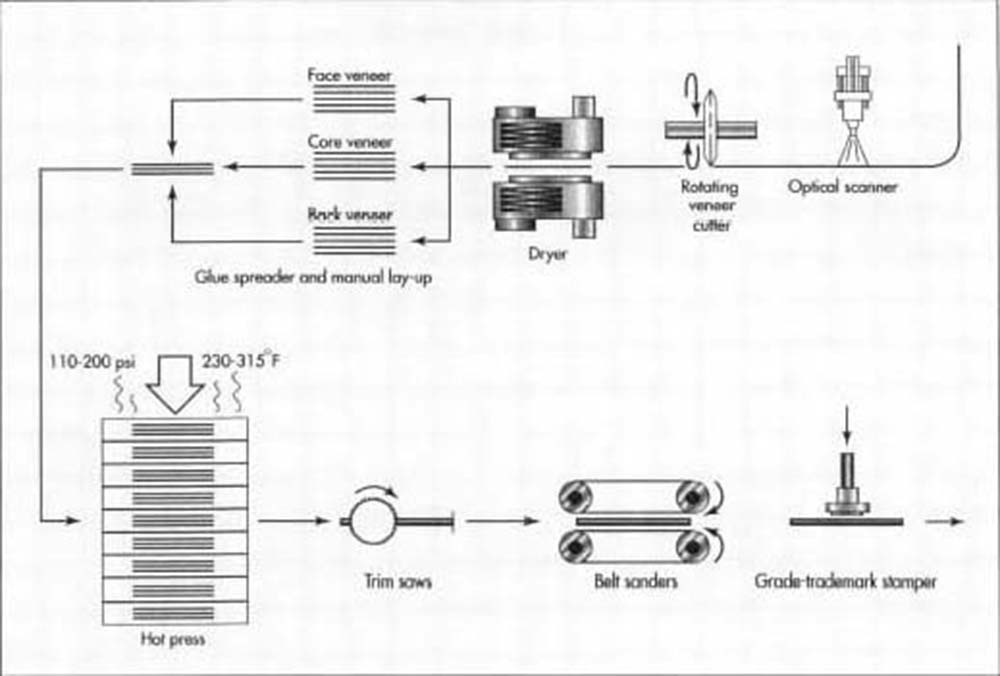
De natte fineerstroken worden op een rol gewikkeld, terwijl een optische scanner eventuele onaanvaardbare defecten in het hout detecteert. Na droging wordt het fineer gesorteerd en gestapeld. Geselecteerde fineerdelen worden aan elkaar gelijmd. Met een hete pers wordt het fineer tot één massief stuk multiplex geseald, dat vervolgens wordt bijgesneden en geschuurd voordat het wordt voorzien van de juiste korrel.
8 De fineerdelen worden vervolgens gesorteerd en gestapeld op kwaliteit. Dit kan handmatig gebeuren, of automatisch met behulp van optische scanners.
9 De gesorteerde secties worden in een droger gevoerd om hun vochtgehalte te verlagen en ze te laten krimpen voordat ze aan elkaar worden gelijmd. De meeste multiplexfabrieken gebruiken een mechanische droger waarin de stukken continu door een verwarmde kamer bewegen. In sommige drogers worden stralen van zeer snelle, verwarmde lucht over het oppervlak van de stukken geblazen om het droogproces te versnellen.
10 Zodra de fineerdelen uit de droger komen, worden ze gestapeld op kwaliteit. Aan de onderbreedtedelen wordt extra fineer bevestigd met tape of lijm. Dit maakt de delen geschikt voor gebruik in de binnenlagen, waar uiterlijk en sterkte minder belangrijk zijn.
11 De delen fineer die kruislings worden geïnstalleerd (de kern in drielaagse platen, of de dwarsbanden in vijflaagse platen) worden in lengtes van ongeveer 1,3 m gesneden.
12 Wanneer de juiste fineerdelen voor een specifieke serie multiplex zijn samengesteld, begint het proces van het leggen en lijmen van de stukken. Dit kan handmatig of semi-automatisch met machines gebeuren. In het eenvoudigste geval van drielaagse platen wordt het rugfineer vlak gelegd en door een lijmkam gehaald, die een laag lijm op het bovenoppervlak aanbrengt. De korte delen kernfineer worden vervolgens kruiselings op de verlijmde rug gelegd en de hele plaat wordt een tweede keer door de lijmkam gehaald. Ten slotte wordt het dekfineer op de verlijmde kern gelegd en wordt de plaat met andere platen gestapeld, klaar om in de pers te gaan.
13 De verlijmde platen worden in een hete pers met meerdere openingen geplaatst. Deze persen kunnen 20-40 platen tegelijk verwerken, waarbij elke plaat in een aparte sleuf wordt geplaatst. Wanneer alle platen zijn geplaatst, perst de pers ze samen onder een druk van ongeveer 110-200 psi (7,6-13,8 bar), terwijl ze tegelijkertijd worden verhit tot een temperatuur van ongeveer 230-315 °F (109,9-157,2 °C). De druk zorgt voor een goed contact tussen de fineerlagen en de warmte zorgt ervoor dat de lijm goed uithardt voor maximale sterkte. Na 2-7 minuten wordt de pers geopend en worden de platen verwijderd.
14 De ruwe platen gaan vervolgens door een set zagen, die ze op de uiteindelijke breedte en lengte afzagen. Platen van hogere kwaliteit gaan door een set 1,2 m brede bandschuurmachines, die zowel de voor- als achterkant schuren. Platen van gemiddelde kwaliteit worden handmatig puntsgewijs geschuurd om ruwe plekken te verwijderen. Sommige platen worden door een set cirkelzaagbladen gehaald, die ondiepe groeven in de voorkant snijden om het multiplex een gestructureerde uitstraling te geven. Na een laatste inspectie worden eventuele resterende defecten gerepareerd.
15 De afgewerkte platen worden voorzien van een kwaliteitsmerk dat de koper informatie geeft over de blootstellingsclassificatie, de kwaliteit, het fabrieksnummer en andere factoren. Platen met hetzelfde kwaliteitsmerk worden in stapels samengebonden en naar het magazijn gebracht in afwachting van verzending.
Net als bij hout bestaat er niet zoiets als een perfect stuk multiplex. Alle stukken multiplex hebben een bepaald aantal defecten. Het aantal en de locatie van deze defecten bepalen de kwaliteit van het multiplex. De normen voor bouw- en industrieel multiplex worden gedefinieerd door de productnorm PS1, opgesteld door het National Bureau of Standards en de American Plywood Association. De normen voor hardhout en decoratief multiplex worden gedefinieerd door de ANSIIHPMA HP, opgesteld door het American National Standards Institute en de Hardwood Plywood Manufacturers' Association. Deze normen stellen niet alleen de kwaliteitssystemen voor multiplex vast, maar specificeren ook de constructie, prestaties en toepassingscriteria.
Hoewel multiplex bomen vrij efficiënt benut – ze worden in feite uit elkaar gehaald en weer in elkaar gezet tot een sterkere, bruikbaardere configuratie – is er nog steeds sprake van aanzienlijke verspilling in het productieproces. In de meeste gevallen wordt slechts zo'n 50-75% van het bruikbare houtvolume van een boom omgezet in multiplex. Om dit percentage te verbeteren, zijn er diverse nieuwe producten in ontwikkeling.
Een nieuw product is Oriented Strand Board (ORPD). Dit wordt gemaakt door de hele boomstam in strengen te versnipperen, in plaats van een fineerlaagje van de stam te pellen en de kern weg te gooien. De strengen worden gemengd met een lijm en samengeperst tot lagen met de nerf in één richting. Deze samengeperste lagen worden vervolgens haaks op elkaar geplaatst, net als multiplex, en aan elkaar gelijmd. Oriented Strand Board is net zo sterk als multiplex en kost iets minder.
Plaatsingstijd: 10-08-2021